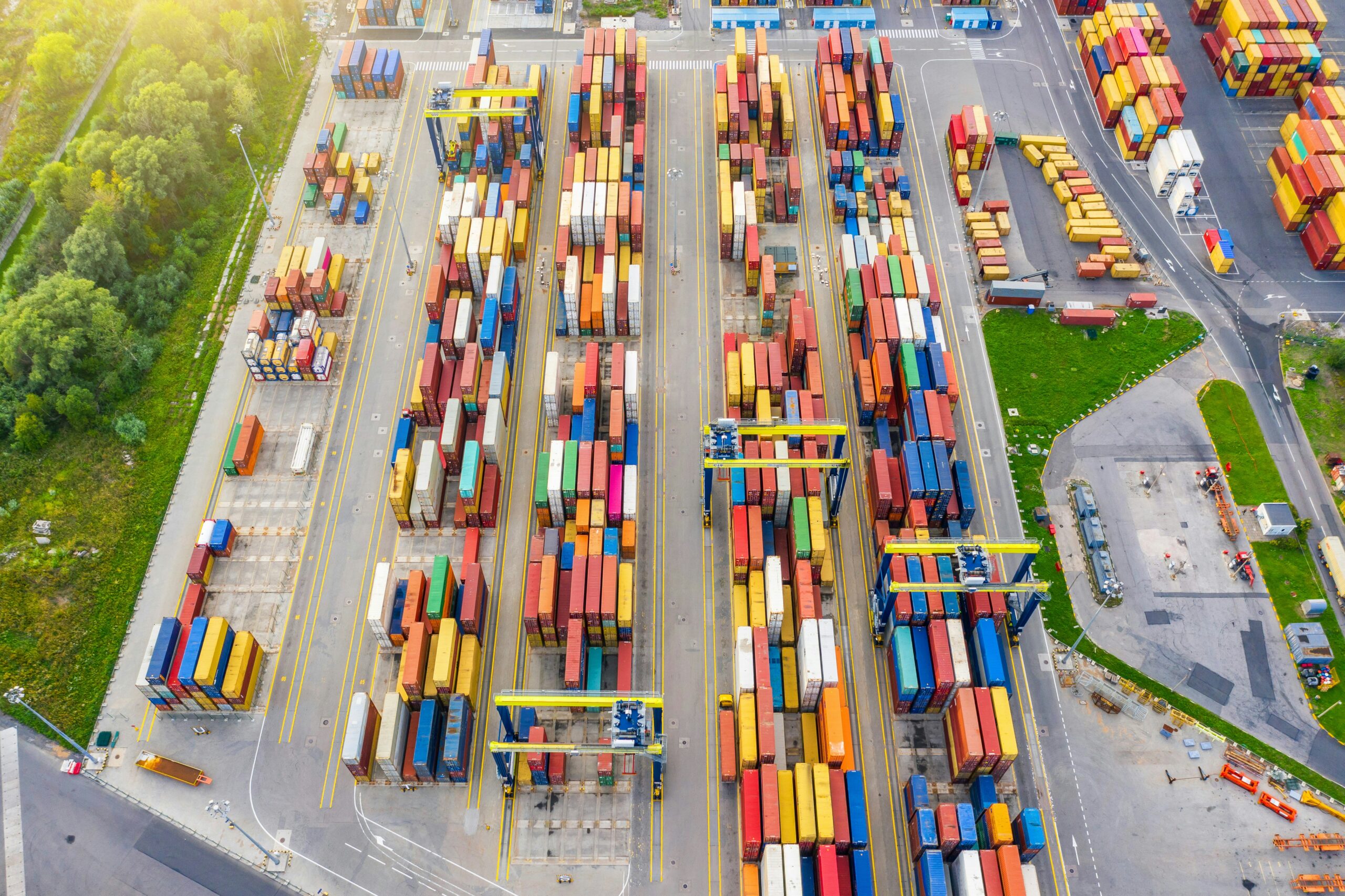
Effective supply chain management (SCM) is a critical factor in the success of any business that produces or distributes goods. One of the most powerful tools to enhance SCM is cost accounting, which allows companies to track, analyze, and allocate costs across the supply chain. With an increasingly complex global marketplace, understanding the cost structure of each supply chain function is essential for improving profitability, efficiency, and decision-making. This article explores how cost accounting supports effective SCM and its impact on business performance.
The Importance of Cost Accounting in Supply Chain Optimization
Cost accounting is a process that tracks and measures all costs associated with producing and delivering goods and services. It includes direct costs such as materials, labor, overhead, and transportation, and indirect costs like warehousing and transportation.
The information gathered from cost accounting allows businesses to identify the most expensive supply chain stages and why. This insight helps to pinpoint inefficiencies and areas where costs can be reduced without sacrificing quality. Whether by optimizing logistics, improving inventory control, or renegotiating supplier contracts, cost accounting provides the data that supports informed decision-making.
By breaking down supply chain costs, businesses can make more strategic decisions that enhance the overall supply chain, improve resource allocation, and boost profitability. Understanding the financial side of supply chain operations allows organizations to manage expenses better while maintaining the ability to meet customer demands efficiently.
Cost Allocation and Its Role in Improving Supply Chain Performance
Cost allocation is a key component of cost accounting. It helps businesses assign specific costs to different activities, departments, or partners in the supply chain. Proper allocation ensures that companies can assess the profitability of each stage of their supply chain, from procurement and manufacturing to logistics and distribution.
Additionally, cost allocation allows businesses to assess the impact of different supply chain strategies. For example, cost accounting data can help a business decide whether outsourcing certain operations or handling them in-house is more economical. This allows companies to evaluate alternatives and make the best decisions for their financial health and supply chain optimization.
Improving Budgeting and Forecasting with Cost Accounting
Accurate budgeting and forecasting are essential for effective supply chain management. Cost accounting is crucial in helping businesses create accurate budgets and predict future supply chain costs. By analyzing historical cost data, companies can forecast how fluctuations in raw material prices, labor costs, or transportation fees may affect the supply chain.
For example, if a business notices that inventory costs have increased in previous months, cost accounting data can highlight why this increase occurred and suggest measures to address the issue, such as implementing just-in-time inventory systems or optimizing stock levels.
By incorporating cost data into budgeting and forecasting, businesses can prepare for future financial fluctuations, avoid stockouts or overstocking, and ensure that supply chain operations run efficiently within economic limits. With better forecasting, companies can avoid potential cost increases and adjust their strategies to maintain profitability.
Identifying Cost-Reduction Opportunities in Supply Chain Operations
One of the main benefits of cost accounting is its ability to identify areas for cost reduction within the supply chain. By breaking down every cost component, businesses can uncover inefficiencies and waste that might go unnoticed.
For instance, cost accounting might reveal that transportation expenses are too high due to suboptimal shipping routes or that inventory holding costs are excessive due to poor warehouse management practices. With this information, businesses can address these issues by negotiating better shipping rates, optimizing routes, or investing in more efficient warehousing systems.
Cost accounting also helps businesses evaluate the trade-offs involved in cost-reduction efforts. For example, a company may weigh the costs of upgrading its supply chain technology versus the potential labor and operational efficiency savings. By analyzing the financial implications of different strategies, cost accounting enables businesses to make decisions that balance cost reduction with long-term improvements in supply chain performance.
Managing Risks with Cost Accounting Insights
Supply chains are susceptible to various risks, including supply shortages, transportation disruptions, and price volatility. Cost accounting can help businesses better understand these risks and develop mitigation strategies.
Cost accounting allows businesses to assess the potential financial impact of disruptions by clearly showing the costs associated with each part of the supply chain. For example, if raw material prices are expected to rise, cost accounting can help a company evaluate how this increase will affect its overall cost structure and profitability.
In addition, cost accounting helps businesses identify areas of risk where cost-saving measures can be implemented. If transportation disruptions are common, companies may invest in alternative transportation methods or sources from different suppliers to minimize cost fluctuations. By proactively managing supply chain risks through cost data, companies can avoid unexpected financial setbacks and maintain smoother operations.
Enhancing Continuous Improvement in the Supply Chain
Continuous improvement in supply chain management is essential for businesses to remain competitive. Cost accounting plays a vital role in this process by providing ongoing data that can be used to evaluate supply chain performance and identify areas for improvement.
Regularly monitoring supply chain costs allows businesses to track performance over time and detect emerging inefficiencies. For example, if transportation costs increase unexpectedly, cost accounting data will help identify the root cause, allowing businesses to adjust before costs spiral out of control.
By using cost accounting as a tool for continuous improvement, businesses can adapt quickly to market changes and improve their supply chain processes. The insights gained from cost accounting help businesses remain agile, reduce costs, and enhance operational efficiency, ensuring they stay competitive in a fast-paced marketplace.
Cost accounting is an indispensable tool in supply chain management, enabling businesses to optimize their operations, reduce costs, and improve profitability. By providing valuable insights into cost allocation, budgeting, forecasting, and risk management, cost accounting supports informed decision-making at every stage of the supply chain. Businesses that leverage cost accounting to identify inefficiencies and opportunities for improvement can achieve more streamlined, cost-effective supply chain operations. In a world where efficiency and cost control are paramount, cost accounting remains a key driver of success in supply chain management.